UV curing is the process by which UV light initiates a photochemical reaction of a UV-curable solution (such as inks, coatings, or adhesives) that causes the solution to polymerize. UV curing (or photopolymerization) is a process that generally happens very fast and virtually instantaneously in some applications, making this technology ideally suited and efficient for high-speed production processes.
What is a UV Curable Coating?
The main components of a UV-curable solution are oligomers, monomers, additives such as pigments for color, and photoinitiators. The oligomers will typically provide the physical properties of the UV-cured polymer, such as hardness vs. flexibility or scratch & scuff resistance. The monomer is generally added as a crosslinking agent to establish the viscosity of the UV-curable solution suitable for the application method. The photoinitiator is a critical ingredient, typically only a few percent of the solution. The component absorbs the UV light and generates free radicals that allow the monomers and oligomers to crosslink together to convert to their hardened polymerized state.
What is UV Light?
Ultraviolet light (UV) is a type of radiant energy that appears on the electromagnetic (EM) spectrum between visible light and x-rays. It has a shorter wavelength than visible light but higher energy (or frequency).
- Wavelength = distance between 2 peaks measured in nanometers.
- Frequency = number of waves over time, measured per second or Hz.
- Short wavelength = high-frequency wavelengths pass in shorter time
- Long Wavelength = lower frequency wavelengths take longer to complete
The EM spectrum has seven regions based on wavelength and frequency/energy.
UV Curing Systems
The complete UV curing system would include a UV lamp housing assembly, power supply (or ballast in the case of an arc lamp), cooling blowers, and cable set to connect the power supply to the lamp. The lamp housing assembly will include the UV bulb with a curved reflector that typically surrounds the UV bulb by 50%-70% and is curved in such a way to either reflect and collimate the UV light toward the substrate for low irradiance exposure or to reflect and focus the UV light for high peak irradiance exposure.
- High Peak Irradiance: Results in a faster cure and greater depth of cure in the UV ink, coating, or adhesive layer. Higher peak irradiance means more UV light photons bombard the top surface, ensuring better adhesion and “through-cure” depth.
Types of UV Systems
Medium-pressure mercury vapor lamps produce UV light for production-scale industrial UV curing processes. Historically, the industry standard for medium-pressure mercury vapor UV lamps used today is arc lamps and microwave-powered electrodeless UV lamps. The choice between these both systems largely depends on the end requirements. Miltec is the only company to provide Arc and Microwave UV systems. Our experts can help you determine the best solution for your application.
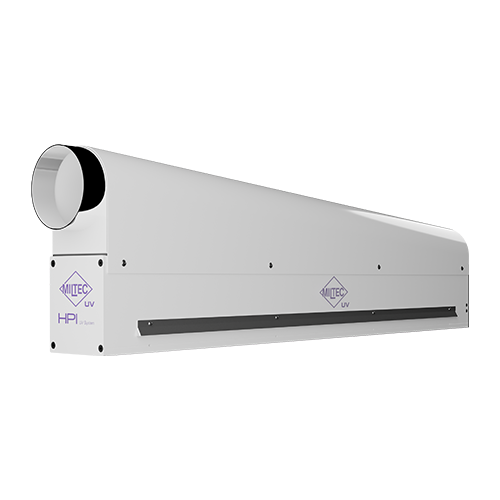
Arc UV System
An arc lamp is constructed with an electrode at each end of a tubular-shaped quartz lamp, typically containing a mixture of mercury and noble gas. When an electrical discharge is applied from the electrodes inside the tubular lamp directly to the mercury, it excites the mercury into a plasma state, which irradiates light over the entire UV spectral range.
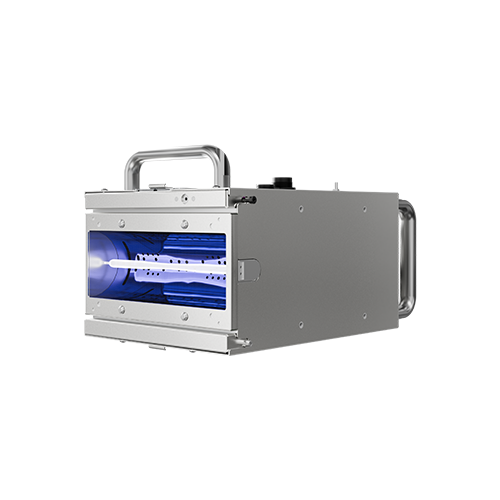
Microwave UV System
The microwave-powered electrodeless UV lamp is also constructed from a quartz tube containing mercury and a noble gas. It is powered by applying microwave energy to the UV bulb, which excites the mercury into a plasma to produce UV light.
Benefits of Arc LamP
•Custom lamp lengths
• Fewer consumable parts
Benefits of Microwave Powered
• Longer bulb life
• Do not require shutters
History of Curing
Before UV curing technology, the conventional method used to dry inks, coatings, and adhesives was large thermal ovens or hot air driers. Thermal drying presents challenges for production plants and the environment. Thermal drying will typically emit VOCs and HAPS into the atmosphere, which can cause health problems for people exposed to these pollutants. Furthermore, thermal drying will normally consume large spaces in a production factory, which is a cost to the user. Large thermal ovens are also costly to operate and maintain.
Advantages of Curing with UV Light
- Faster Cure Speeds: Compared to thermal drying methods.
- Energy Efficient: Consumes less energy than thermal drying.
- Environmentally Friendly: UV-curable solutions are typically 100% solids, eliminating the need for solvent recovery systems.
- Space-Saving: UV lamps occupy less floor space than thermal ovens.
- Higher Quality Products: Results in clearer printed materials.
Industries
UV curing can be used in almost any application that involves applying a coating or ink to any product to improve the physical characteristics of that product or for decorating the product and improving its aesthetics. It can be used for products in flat sheet form or 3-D shapes. Some typical UV applications are as follows: