UV curing reflectors typically have a semi-elliptical or parabolic geometry that wraps around the upper half and runs the entire length of the UV bulb. These lamp reflectors are an essential part of the UV system because they are responsible for reflecting about 65% of the UV energy emitted from the UV bulb to the customer’s product.
When the UV reflectors are not cooled properly, they can warp and wrinkle due to thermal expansion. The photo below shows what an overheated UV reflector looks like.

The reflectors’ curved shape concentrates (or focuses) the light rays to a very small target area, creating extremely high UV peak irradiance at the customer’s product, which is one of the keys to UV curing.
UV Reflectors that lose their curved shape will cause the reflecting light ray pattern to become scattered or diffused from the target product and could result in a partial cure.
The graphic below shows two conventional light ray patterns used in most UV curing systems. It is essential that the curved shape of the reflector remain throughout lamp operation to maintain these patterns.
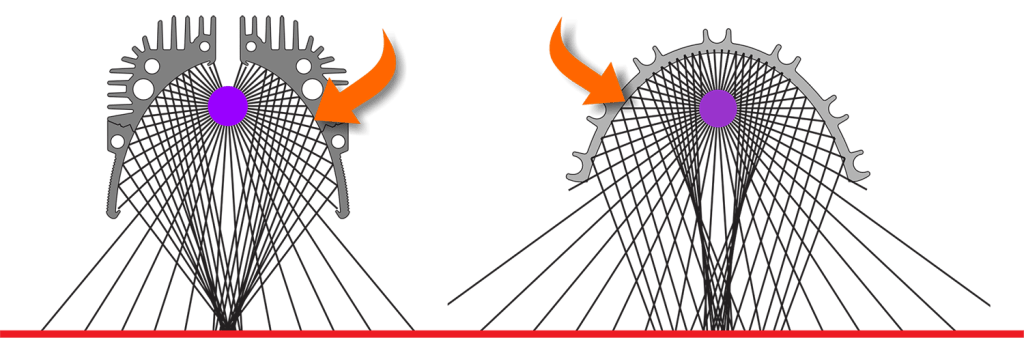
In addition to maintaining the desired reflector curve, routine maintenance is also extremely important for UV reflector efficiency. When the reflectors become dirty, contaminated, or dulled over time, the percent of reflectivity decreases significantly, reducing the UV energy and intensity delivered to the customer’s product. In almost all cases, a dirty or dulled reflector will actually have more impact on UV output than an old or poorly performing UV bulb.
The UV reflector is considered a consumable part of all UV systems. It requires attention and maintenance (or periodic cleaning) to help ensure good consistent UV output from the UV lamp system. Some UV systems use replaceable reflector liners, which are a thin polished aluminum material with a protective coating (which looks much like a conventional mirror finish) and typically pre-curved and cut to fit into a reflector holder inside the lamp housing.
Other more sophisticated UV lamps use “cold mirror” reflectors, which are also thin, pre-curved, and cut aluminum or glass reflectors positioned in a holder of some type inside the lamp housing. Cold mirror reflectors have special coatings applied to the reflective side of the reflector substrate that are designed to efficiently reflect UV light but also absorb the IR energy (heat) emitted by a UV bulb. Cold mirror reflectors reduce the heat load on the customer’s product as it travels under the UV lamps.
Other less sophisticated UV systems use a polished aluminum extrusion as the reflector, which is curved around the UV bulb and acts as a reflector and a lamp shutter. Regardless of the reflector type, it is important that the reflector always maintains a clean, shiny appearance.
If the reflector begins to look dull or dirty, it needs to be either cleaned or replaced. Reflectors should be cleaned using a lint-free cloth, isopropyl alcohol, or a surface cleaner that does not leave a film. Cleaners that contain ammonia are not recommended. If the reflector still appears dull or dirty after cleaning, it should be replaced.
Measuring your UV output will also help diagnose a poor-performing reflector. The best device to measure UV output is a “puck” style radiometer that measures UV light energy in all 4 UV ranges: UVA, UVB, UVC, and UVV.
The puck-style radiometer is placed on the conveyor belt and run under the UV lamp at some pre-defined constant speed, and it will measure the total UV energy delivered by the lamp. When the UV energy reduces to a point where you are in danger of not achieving proper cure, then it is most likely time to clean and/or replace the lamp reflector.
Whether visible or measurable via a radiometer, monitoring UV reflectors are important to maintaining a consistent cure. If you are experiencing issues with UV output, you might want to consider Miltec’s free UV Performance Check. Our UV system check will include the inspection of your UV system and may include radiometer readings showing the output and performance of your UV system with the goal of identifying which parts that may need to be replaced to ensure maximum UV output of your lamp system. We can also provide recommendations for preventive maintenance tasks to help ensure consistent UV performance for years to come. Learn more and request your Performance Check today.
In our next Maintaining UV System Performance post, we’ll explore Ballasts & Bulbs.